Better Visibility & Intelligence for Warehouse, Yard, and Facility Assets
Improve utilization of Kanban bins, forklifts, molds, facility assets, and truck turnaround times in a yard, and accurately forecast production and shipping times to offer firm delivery commitments. Enhance customer experience with a precise, real-time work-in-process (WIP) order status in a manufacturing line or at a warehouse with a click of a button.
Comprehensive Solutions for Diverse Industries
Harness the power of our end-to-end solutions, tailored to meet the unique demands of various sectors, ensuring efficiency, reliability, and excellence in every step.
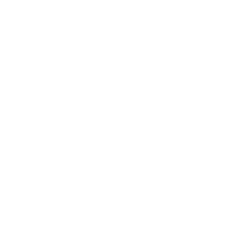
Electronics
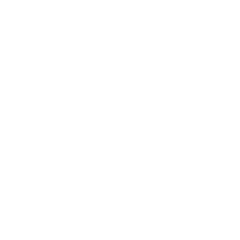
Automotive
Challenges with Warehouse, Yard, and Facility Asset Visibility
The standard practice for tracking manufacturing velocity and dwell/detention times in warehouses and yards tends to be inefficient, resulting in various challenges.
CHALLENGE #1
RFID's "line of sight" requirement for accurate reads and extensive infrastructure requirement in the facility.
CHALLENGE #2
RFID’s dependence on standard operating procedures for movement of Kanban bins, molds, forklifts, etc.
CHALLENGE #3
Lack of live data visualizations on process chokes, manufacturing velocity, and ship date ETA changes.
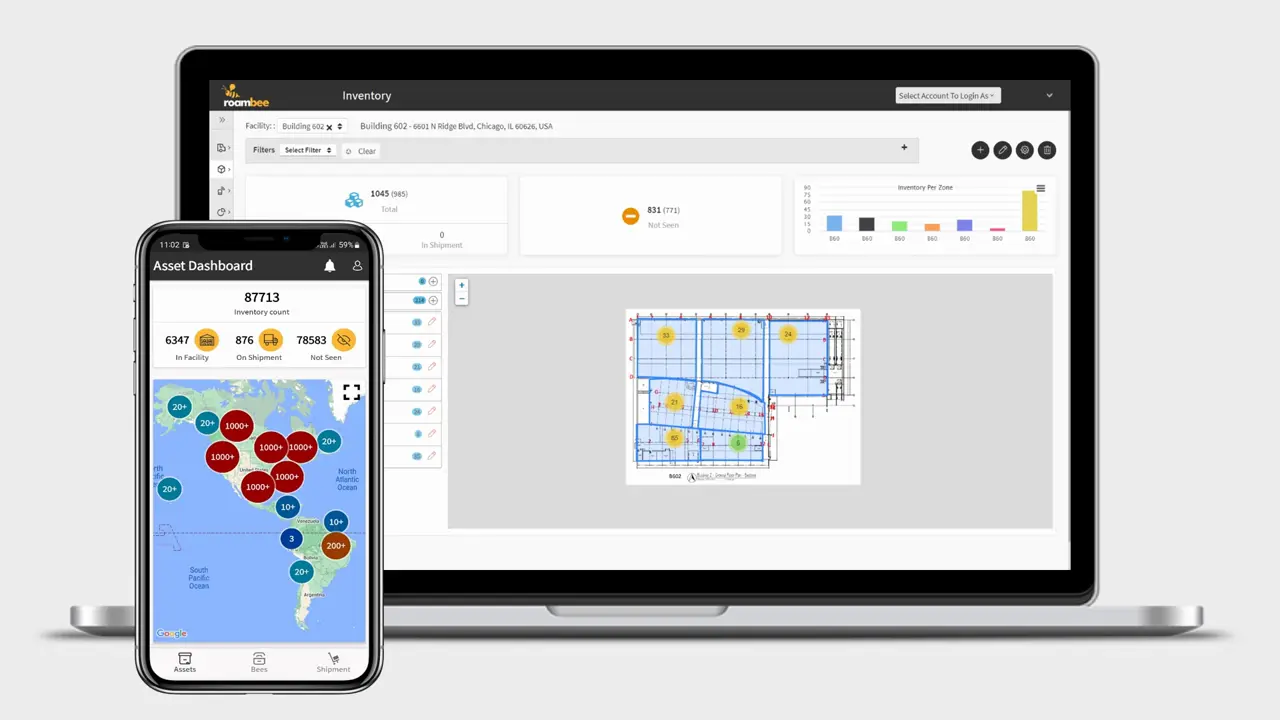
How Roambee's Solution Works for Warehouse, Yard, & Facility Assets
Visibility
Better visibility by combining production planning, WMS, TMS, and order information with real-time, zone-level location and condition data of Kanban bins, molds, sub-assemblies, or finished goods tagged with IoT sensors.
Alerts & Signals
Built on verifiable visibility, alerts & signals empower better decisions and drive automation. For example, a business signal on work-in-process (WIP) status is derived by sensing the manufacturing milestone/stage to enable timely order shipping.
Intelligence
Use AI-powered network insights & foresights for better supply chain planning & execution. For example, assess production line chokepoints by zone, SKU, and factory and forecast this key performance indicator (KPI).
Experience the Power of Roambee
Experience the Power of Roambee
Alerts & Signals to Help You Make the Right Decisions
Strengthen your decision-making capabilities with real-time alerts and actionable insights, ensuring efficient responses to any challenges or deviations in the management of your warehouse, yard, and facility assets
Asset Signals
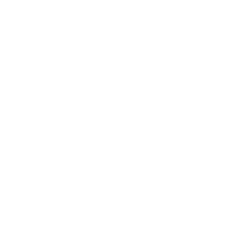
Location & Geofencing
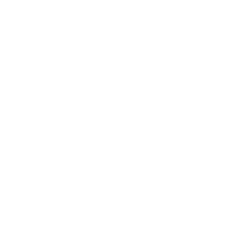
Line Stage or
Milestone Completion
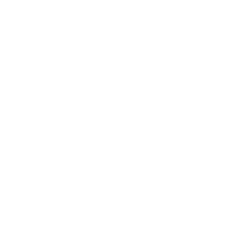
Facililty Asset
Utilization
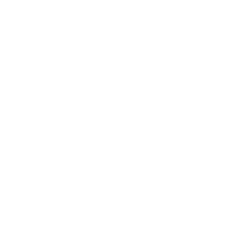
Facililty Asset
Dwell Time/Aging
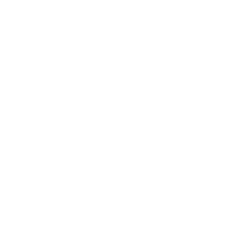
Location & Geofencing
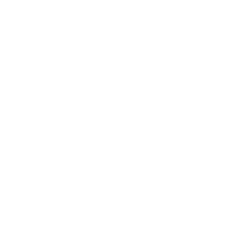
Line Stage or
Milestone Completion
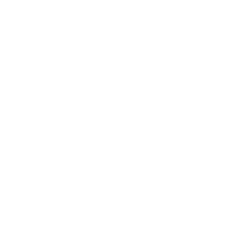
Facililty Asset
Utilization
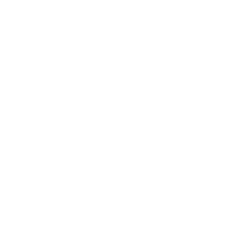
Facililty Asset
Dwell Time/Aging
Business Signals
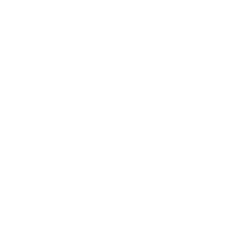
Full/Empty Status
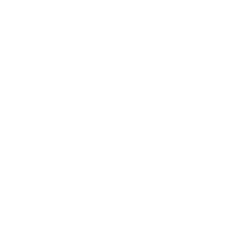
Manufacturing ETA
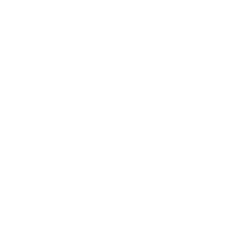
Order Ship Date ETA
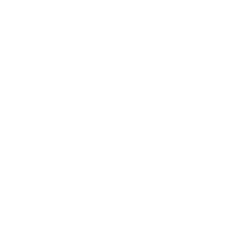
Full/Empty Status
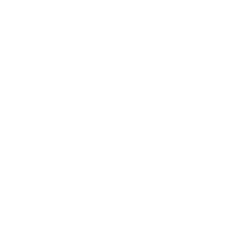
Manufacturing ETA
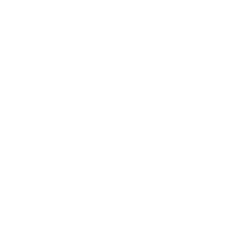
Order Ship Date ETA
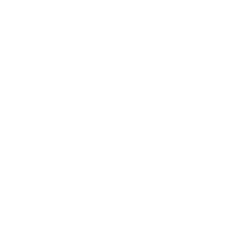
Loss/Theft of Assets or Asset Groups
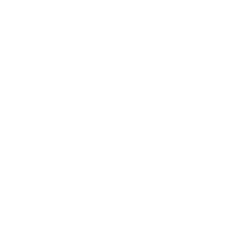
Unauthorized Use of Assets or Asset Groups
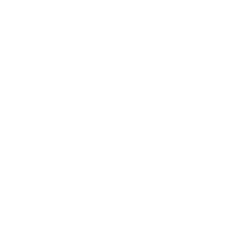
The Aging of Assets or Asset Groups
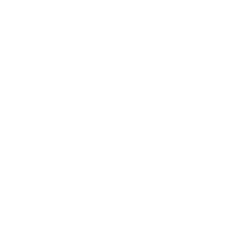
Production Line Chokepoints
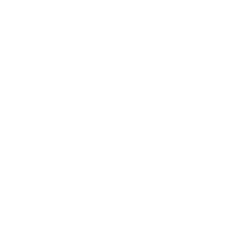
Warehouse/Yard Dwell Time
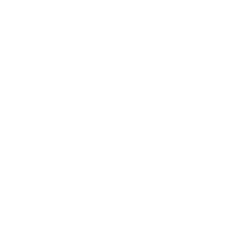
The Aging of Assets or Asset Groups
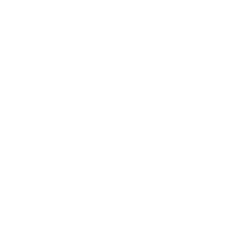
Cold Chain Compliance Prediction of Shipments Carried by Assets
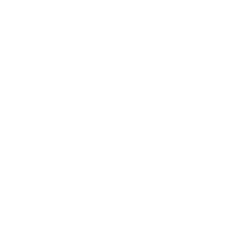
Manufacturing Velocity & Warehouse Throughput
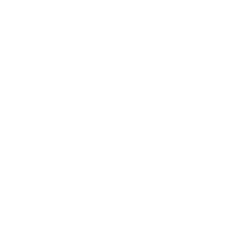
Job Progress or Work-in-Process (WIP) Components Availability
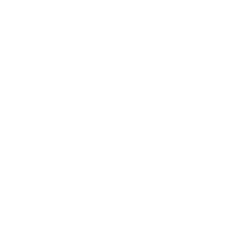
Cold Chain Compliance Prediction of Shipments Carried by Assets
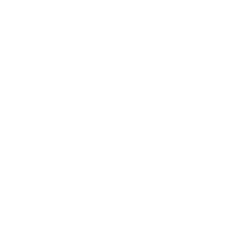
Manufacturing Velocity & Warehouse Throughput
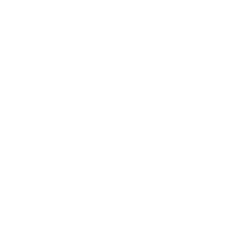
Job Progress or Work-in-Process (WIP) Components Availability
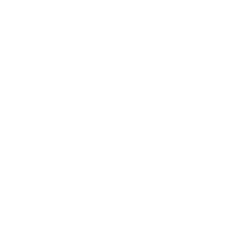
Production Line Chokepoints
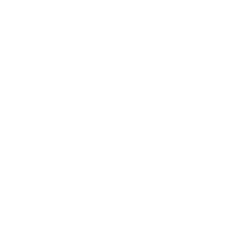
Warehouse/Yard Dwell Time
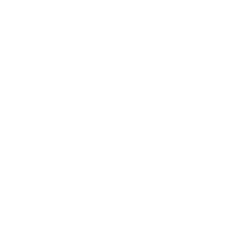
Loss/Theft of Assets or Asset Groups
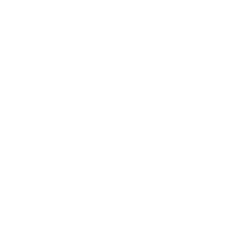
Unauthorized Use of Assets or Asset Groups
Business Outcomes with
Roambee
Business Outcomes with Roambee
Revitalize your asset management with Roambee. Deliver firm delivery commitments, boost manufacturing velocity, and optimize the utilization of facility assets. Achieve faster turnaround times and elevate your customer experience with timely and accurate order shipping.
- Improve your customer experience with firm delivery commitments by forecasting work-in-process (WIP) inventory status at production or warehousing stages and ship date ETAs.
- Improve manufacturing velocity and warehouse/yard throughput with better inventory management.
- Utilize Kanban bins, molds, forklifts, and other facility assets effectively to reduce your asset investment at scale.
- Compress turnaround times (TAT) in packaging, storage, yard, and shipping operations.
Empowering you with our Intelligence
Unlock the power of AI-powered insights for asset management. Dive deep into processing times, manufacturing chokepoints, and SLA violation patterns. With Roambee’s foresights, anticipate ship date ETAs, stage completion timelines, and potential SLA violations.
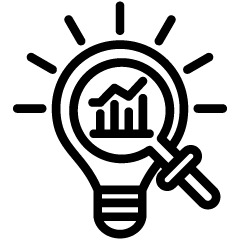
Insights
- Production or warehouse/yard processing time by stages.
- Chokepoints in the manufacturing line or warehouse/yard and across factories.
- SLA violation patterns in movement of Kanban bins, forklifts, molds, or sub-assemblies.
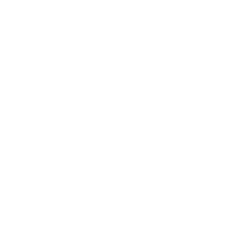
Foresights
- Ship date ETA prediction for SKUs.
- Stage completion ETAs in manufacturing.
- SLA violation predictions of assets by zone or facility.
Optimizing Assembly Lines for a Leading Automotive OEM
- About: A major automotive OEM faced challenges with inefficiencies and choke points in their sub-assembly lines, leading to inaccurate production schedules and downstream delays in logistics and order fulfillment.
- Roambee's Intervention: Using Roambee's intelligence, the company identified a significant variance (about 57%) between the slowest and fastest processes. A deeper analysis revealed that optimizing just two lines by 18% would synchronize all sub-assembly lines, preventing inventory build-ups.
- Results: The targeted optimizations led to streamlined sub-assembly processes and reduced inventory pileups.
- Impact: The company achieved synchronized production, improved logistics planning, and timely order fulfillment.
Resources on Visibility & Intelligence
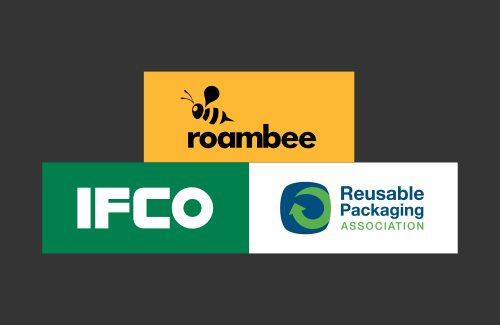
Webinar
How IFCO Has Found The Missing Piece Critical To Your Supply Chain
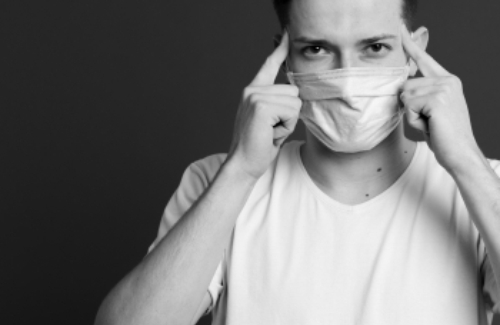
E-book
Making Smart Supply Chain Decision in the New Normal
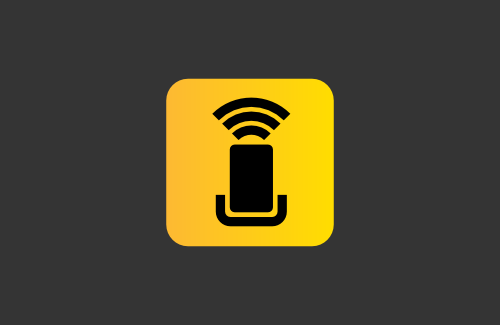