Better Visibility & Intelligence for Food Cold Chains
Deliver temperature-sensitive food products on time and in full (OTIF), deliver on your brand’s quality promise, and ensure availability on shelves with active monitoring and early warning signals to mitigate business disruptions across land, air, and ocean for all ambient, refrigerated, and frozen goods.
Challenges with Food Cold Chain Visibility
For tracking the food cold chain, the prevalent method is using passive or active data loggers, which comes with its own set of challenges.
CHALLENGE #1
Manual touchpoints in passive data logging making data capture delayed and unusable for preventive action.
CHALLENGE #2
Visibility is limited to basic location and condition, even if the data captured is in real-time.
CHALLENGE #3
Inability to identify the root cause of excursions nor foresee the impact on quality control (QC) or stock planning.
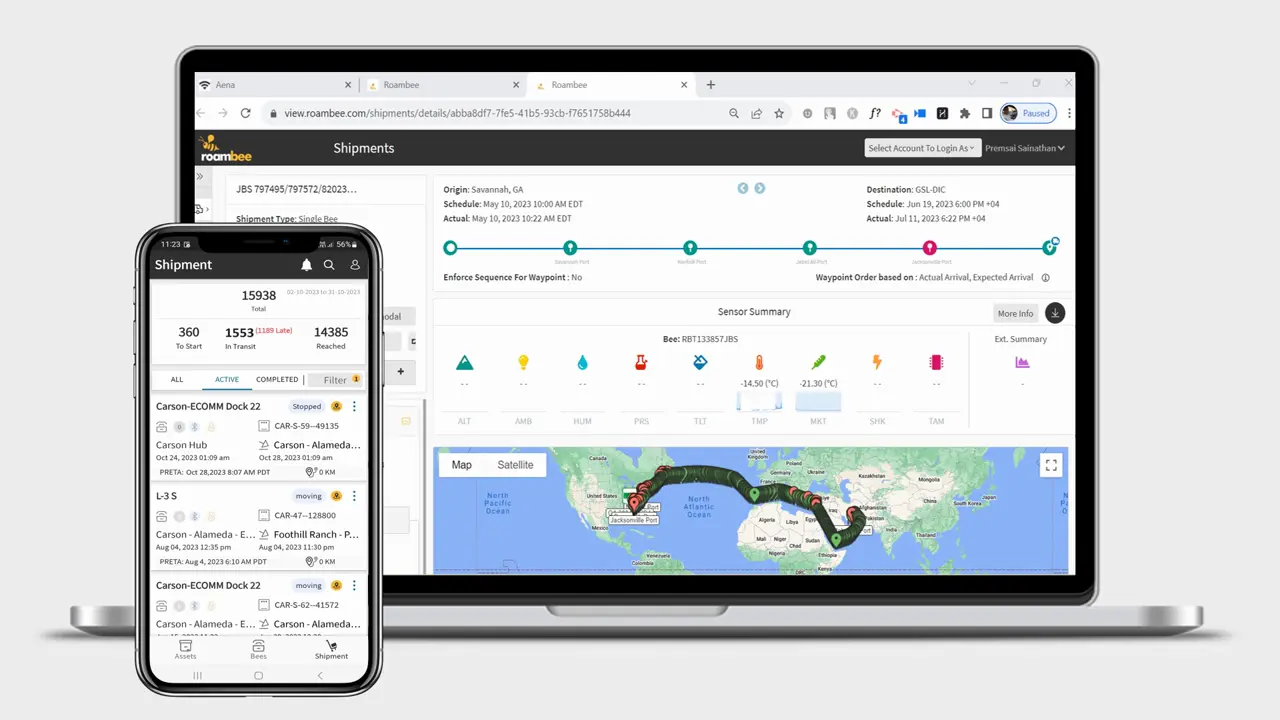
How Roambee's Solution Works for Food Cold Chains
Visibility
Better visibility by combining order information with real-time location and condition data from IoT sensors and data streams from port/airport operations, vessel/airline traffic, freight forwarders, and carrier data aggregation platforms.
Alerts & Signals
Built on verifiable visibility, alerts & signals empower better decisions and drive automation. For example, a business signal about quality compliance (QC) is derived by sensing temperature and handling, enabling you to mitigate supply risk.
Intelligence
Use AI-powered network insights & foresights for better supply chain planning & execution. For example, score quality compliance (QC) performance by lane, carrier, port, and airport and forecast this key performance indicator (KPI).
Experience the Power of Roambee
Experience the Power of Roambee
Alerts & Business Signals to Help You Make the Right Decisions
Empower your decision-making with real-time alerts and actionable business insights, ensuring timely responses to any disruptions or anomalies in your food cold chain operations.
Shipment Signals
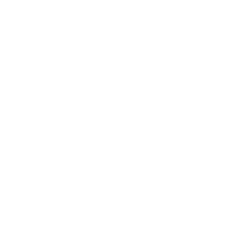
Loading & Unloading
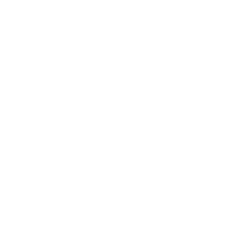
Departure & Arrivals
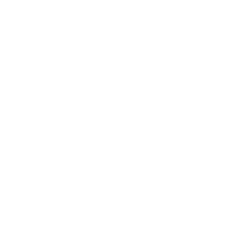
Route Deviation
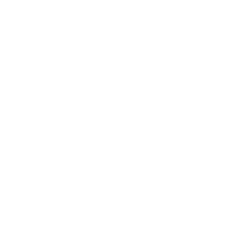
Customs Clearance
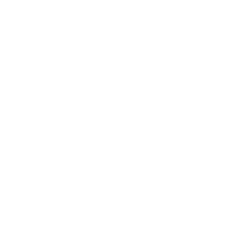
Electronic Proof of
Delivery (ePoD)
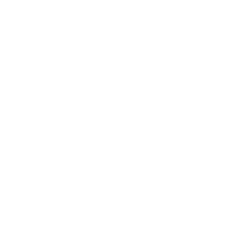
Temperature & Humidity
Excursion
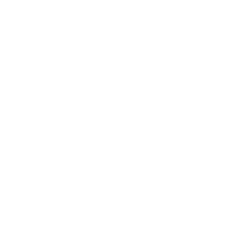
Mean Kinetic
Temperature (MKT)
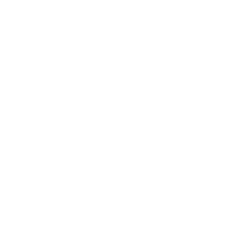
Time Out of
Refrigeration (TOR)
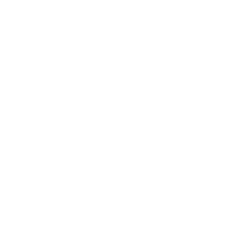
Tilt & Shock
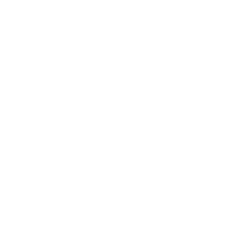
ETA & Delay Signals
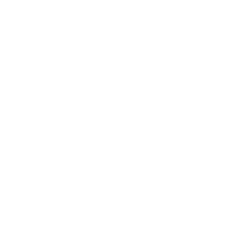
Pick-up & Delivery
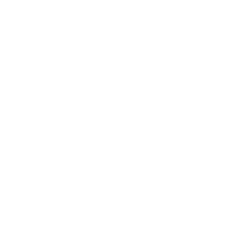
Location & Geofencing
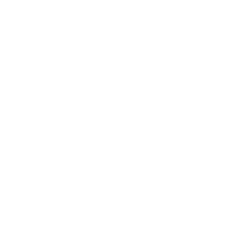
Authorized & Unauthorized
Container Door Opening
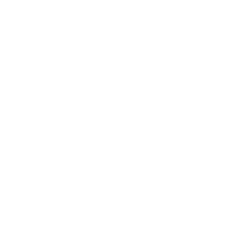
Authorized & Unauthorized
Package Opening
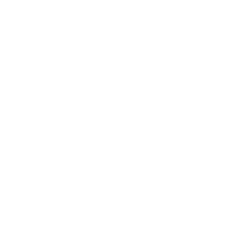
Storage
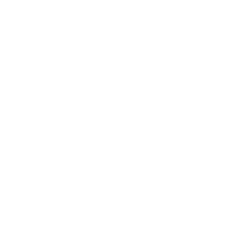
Security Screening
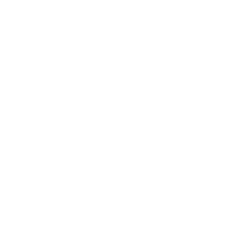
Loading & Unloading
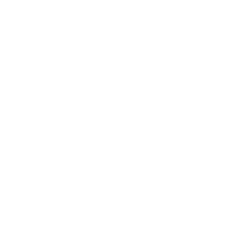
Departure & Arrivals
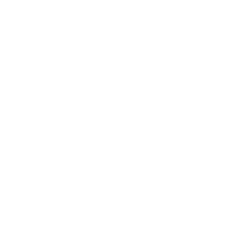
Route Deviation
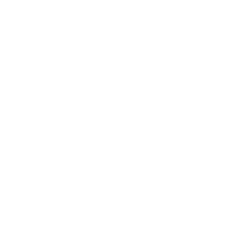
Customs Clearance
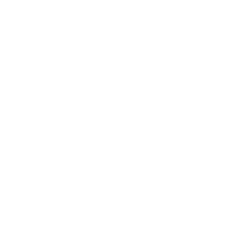
Electronic Proof of
Delivery (ePoD)
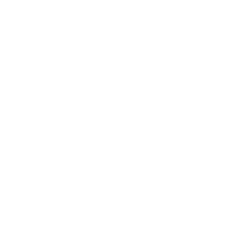
Temperature & Humidity
Excursion
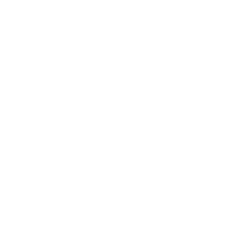
Mean Kinetic
Temperature (MKT)
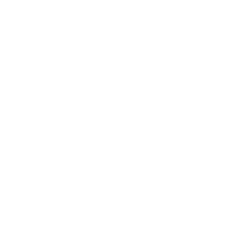
Time Out of
Refrigeration (TOR)
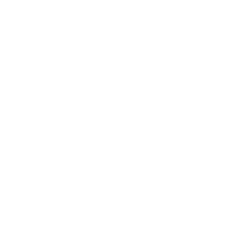
Tilt & Shock
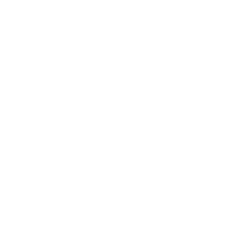
ETA & Delay Signals
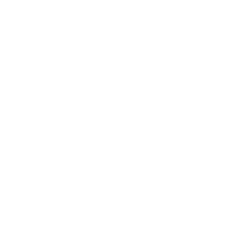
Pick-up & Delivery
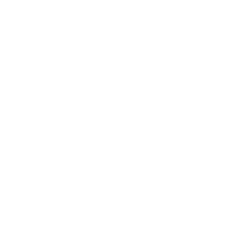
Location & Geofencing
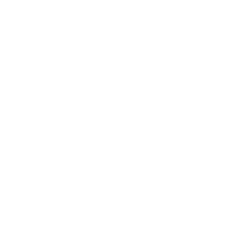
Authorized & Unauthorized
Container Door Opening
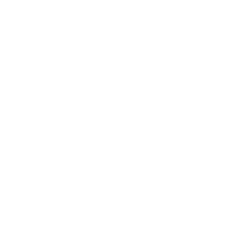
Authorized & Unauthorized
Package Opening
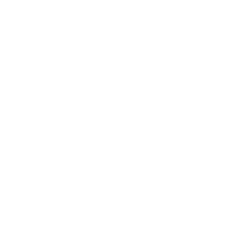
Storage
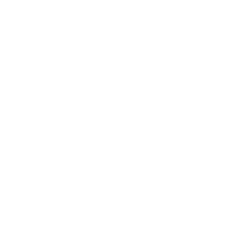
Security Screening
Business Signals
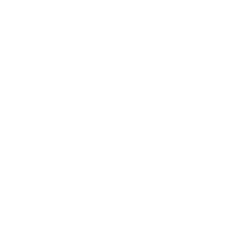
Delivery Time Windows
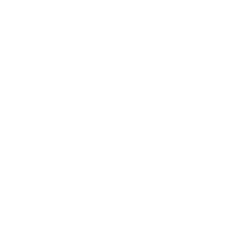
Order Fulfilment
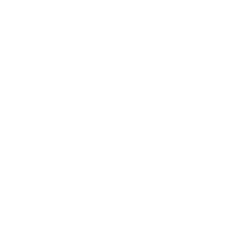
Revenue Recognition
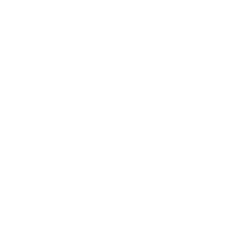
Delivery Time Windows
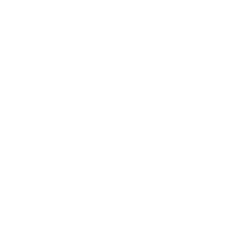
Order Fulfilment
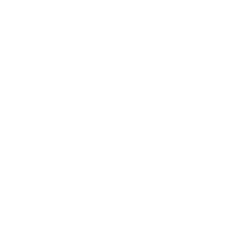
Revenue Recognition
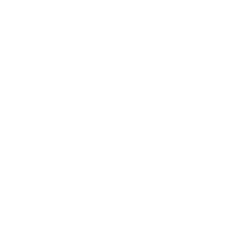
Cold Chain Compliance Prediction
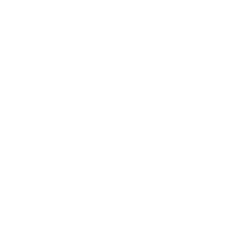
Chain of Custody Breaches
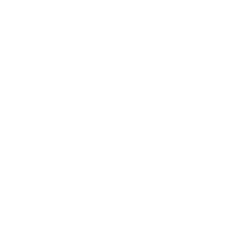
Cargo Handling (Damage)
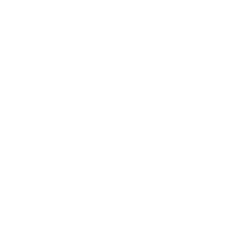
Cold Chain Compliance Prediction
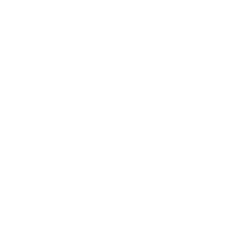
Chain of Custody Breaches
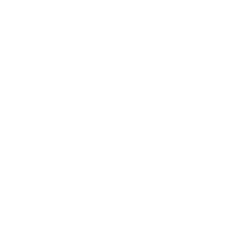
Cargo Handling (Damage)
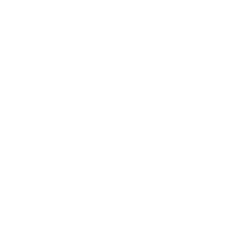
Airport Operations Anomalies: Consolidation, Wrong/Missed Connections, Customs, etc.
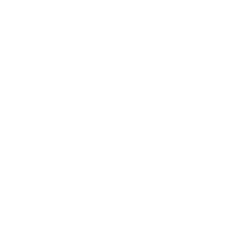
Port Operations Anomalies: Wrong/Missed Connections, Customs Processing, etc.
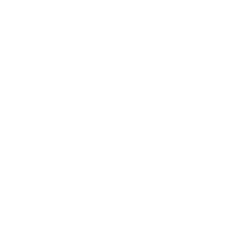
Flight Connections Through Unauthorized Countries
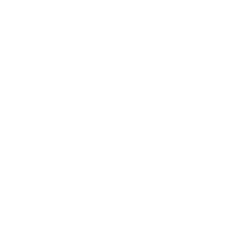
Airport Operations Anomalies: Consolidation, Wrong/Missed Connections, Customs, etc.
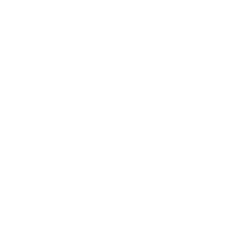
Port Operations Anomalies: Wrong/Missed Connections, Customs Processing, etc.
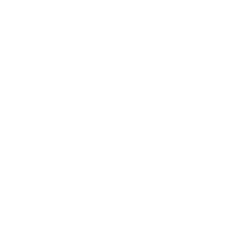
Flight Connections Through Unauthorized Countries
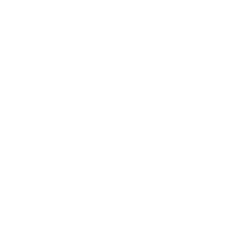
Shipment Security Risk
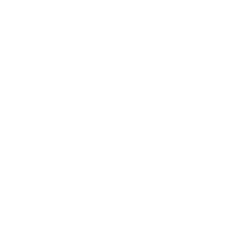
Shipment Security Risk
Business Outcomes with Roambee
Business Outcomes with
Roambee
Revolutionize your food cold chain operations with Roambee. Ensure “farm-to-fork” transparency, achieve flawless order fulfillment, and drive sustainability. Boost revenue, reduce food wastage, and ensure consistent availability of your brand on retail shelves.
- "Farm-to-fork" transparency for customers and better sustainability with lesser food wastage/CO2 emissions.
- Automate the quality control (QC) and proof of delivery (PoD) processes remotely for delivery fulfillments worldwide.
- Mitigate food quality degradation, contamination, or security compromises in the chain of custody by consistently achieving cold chain compliance scores above 80%.
- Increase revenue by always ensuring the availability of your brand on retail shelves.
Empowering you with our Intelligence
Unlock the potential of AI-powered insights for food cold chains. Delve into performance metrics, understand operations, and predict challenges. With Roambee, navigate risks, refine your supply chain, and consistently achieve QC and OTIF targets.
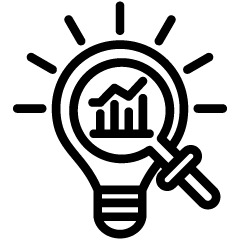
Insights
- OTIF performance scoring by lanes, carriers, and nodes.
- Quality compliance (QC) performance across lanes, carriers, and nodes for cold chain and handling.
- Dwell-time/Turnaround-time (TAT) insights into airports, ports, and transshipment operations.
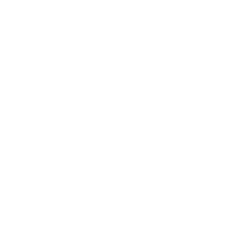
Foresights
- Supply risk prediction at any given node on any given day.
- OTIF and cold chain compliance SLA (service level agreements) predictions by lanes and carriers.
- Handling and security risk predictions at airports, ports, transshipment locations, and during the first/last mile.
Elevating Cold Chain Compliance for a Renowned European Chocolatier
- About: A distinguished European chocolatier aimed to make their supply chain resilient against seasonal challenges, especially in warmer regions.
- Roambee's Intervention: Through Roambee's insights, the top 20 lanes out of 93 in the APAC region were identified, which accounted for over 60% of their cold chain compliance breaches.
- Results: With targeted interventions, the chocolatier boosted their compliance rate from 59% to over 85% compared to the same season in the prior year.
- Impact: The company upheld its brand promise, enhanced sustainability, and minimized costs from wastage due to rejected goods.
Resources on Visibility & Intelligence
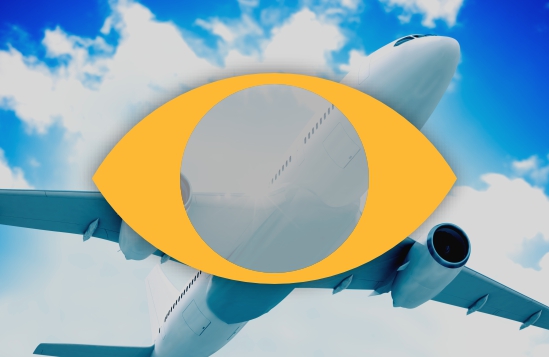
Webinar
Part 1: Telematics Aggregation vs. Sensor Driven Supply Chain Visibility
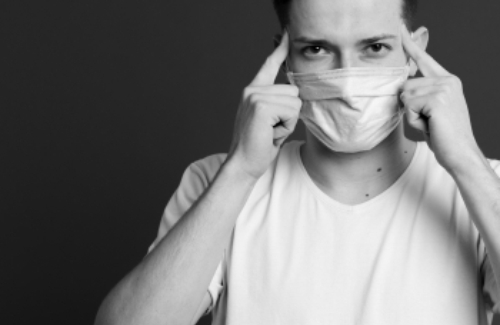
E-book
Making Smart Supply Chain Decision in the New Normal
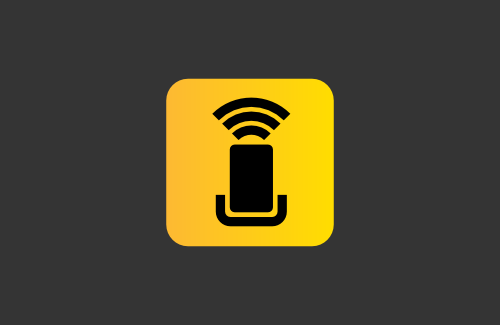